Our valves can
sweeten your life
In the home of Apfelstrudel apple cake and Kaiserschmarrn sweet pancakes, it is clear that there is also a significant sugar industry in the country. 5,800 sugar beet farmers supply about two million tonnes of sugar beet annually, from which around 500,000 tonnes of sugar are produced in Austria’s sugar factories.
The two major plants in Austria’s sugar production and other plants in Hungary, the Czech Republic, Slovakia, Bosnia-Herzegovina and Romania are equipped with Flowtec valves.
In the starch industry as well, Europe’s leading supplier relies on our valves, which we deliver to their plants in Austria and Eastern Europe.
We therefore know about the process technologies that extract starch from one third of Austria’s potato harvest for the food industry and the textile and paper industries and convert the sugar beet into sugar. We can use this knowledge specifically to recommend efficient and long-lasting solutions to our customers in the sugar industry and in starch production, thus helping them to achieve a trouble-free working day.
Our top-products for sugar & starch production
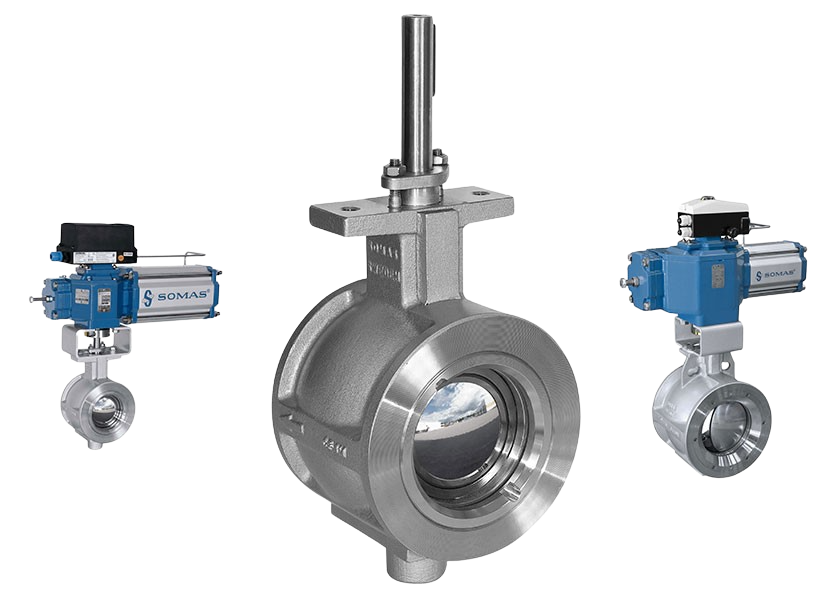
Ball segment valve, wafer design, standard face-to-face dimension
“The unique system of a shaft with a clamping coupling was developed by Somas for backlash-free torque transmission and enables extremely precise control behaviour.
The valve body of the Somas wafer type ball segment valve KVTW-A / KVXW-A is produced in one piece.
The spring seat is available in three material alternatives (PTFE, PTFE 53 and HiCo [high cobalt alloy]).
The type KVTW with a centrically mounted shaft, as well as the type KVXW with an eccentrically mounted shaft are produced in a wafer version. The A-version of the valve is produced in the standard long lengths typical of the market.
The valve is also produced in the D-version with a shorter length (see Si-114).
“
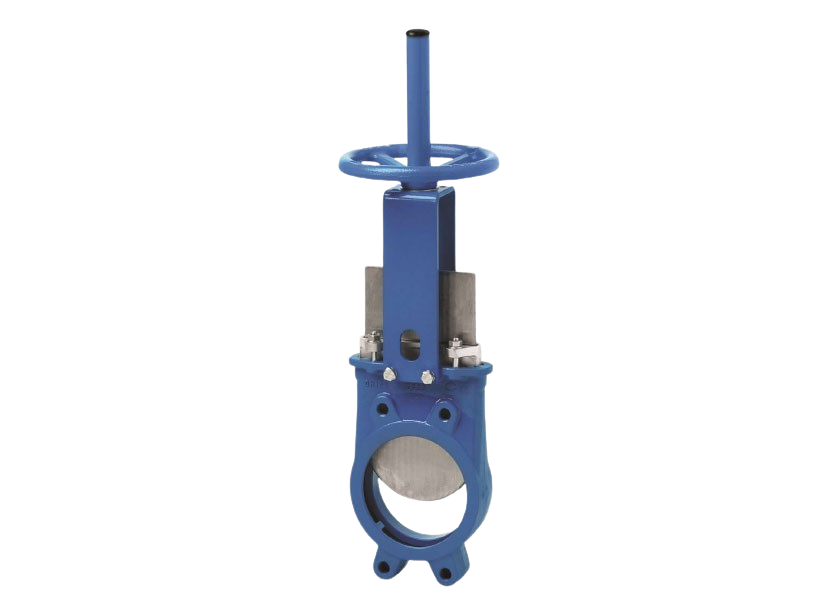
Uni-directional knife gate valve
“The standard knife gate valve type EX from Orbinox is a uni-directional wafer valve. It is suitable for general industrial applications.
The design of the housing and seat ensures blockage-free shut-off when using suspended solids in many industrial sectors.”
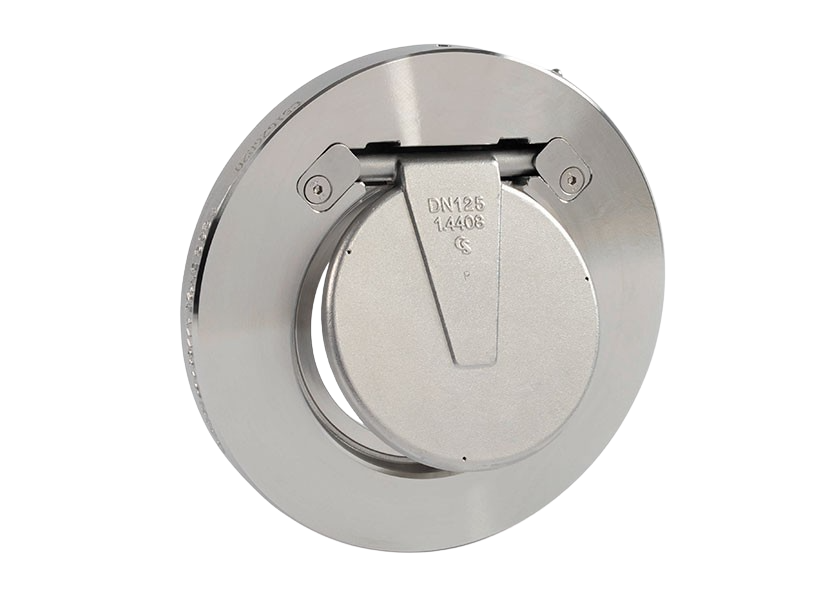
Wafer type swing check valve
The check valve CSC / CSCF offers efficient performance in a small space.
A robust shaft and a defined end stop guarantee an above-average service life. The angled shaft seat ensures improved seat tightness even at low pressures. The valve can also be equipped with a spring that supports the closing process. The large number of turns of the optional spring prevents overloading and guarantees long-lasting durability.
The check valve CSC / CSCF can be used in all industrial processes with liquids, gases and steam.
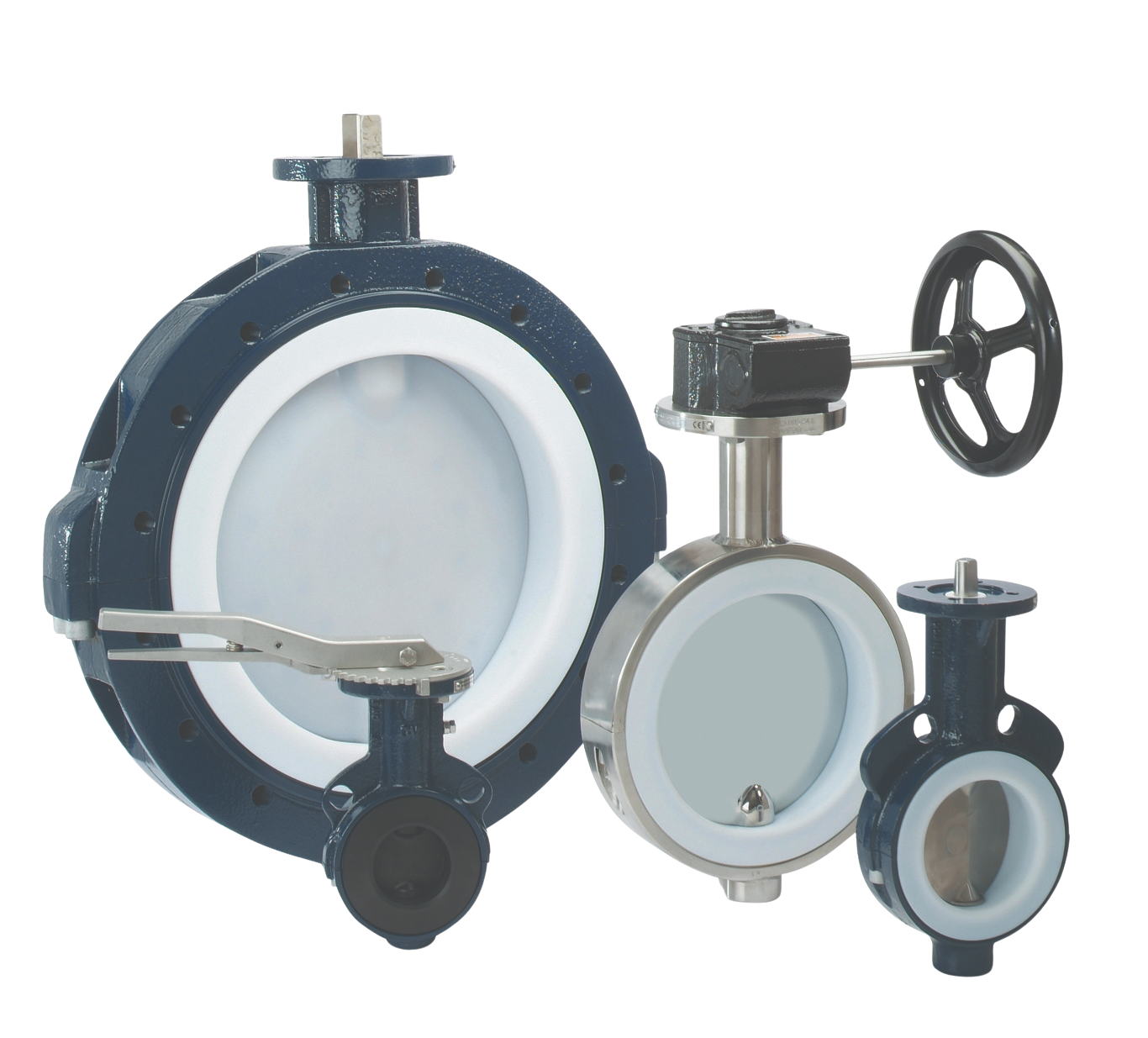
PTFE lined butterfly valve
The ChemValve-Schmid butterfly valve CST is the world’s leading modular PTFE lined butterfly valve.
The PTFE lined valve is produced to the highest quality standards for the safe handling of aggressive media. It is designed for the use with highly chemical media and is therefore used in almost all industries.
Spherical structural elements reduce friction and therefore increase the service life.
Where our valves
make the processes strong.
Ceramic valves face the toughest conditions, such as abrasive limewash, anti-caking agents and other aggressive media. In the sugar and starch industries, the particularly robust valves must withstand high switching cycles and often have a long service life. Highly viscous media are the norm in the production process for sugar and starch production, whereby the special physical properties of starch further increase the requirements.
Steam and high temperatures are naturally also present in processes in the sugar and starch industries. For example, our metal seated ball valves or individually selected butterfly valves are used here.
The hot water / steam applications in starch production require precise control, which we guarantee with our Somas ball segment valves.
It goes without saying that we can supply the appropriate valves with the required FDA approval.
When little things
make a big difference!
In many areas, only the obvious requirements are taken into account when selecting valves. What is often not immediately obvious is that with smaller nominal diameters a considerable cost saving can be achieved.
We always design our valves according to the respective process data. With our control valves, such as the Somas ball segment valves, downsizing is quite simple. We also offer special solutions with optimised nominal diameters for other products at an attractive price/performance ratio.